Flexium+68 und das Kampfflugzeug Rafale
Die kommerziellen Erfolge des Geschäftsreiseflugzeugs Falcon reissen nicht ab. Was das Modell Rafale angeht, konnten in letzter Zeit ebenfalls Exporterfolge erzielt werden, die das hohe Leistungs- und Technologieniveau des Flugzeugs erwartungsgemäss bestätigen. Für den Hersteller Dassault Aviation sind diese Erfolge natürlich begrüssenswert, jedoch stellen sie das Unternehmen auch vor industrielle Herausforderungen. Das klar formulierte Ziel lautet: Zu den vereinbarten Lieferzeiten die von den Kunden erwartete Qualität zu realisieren.
Am Standort von Dassault im französischen Biarritz stellt man sich dieser Herausforderung. Das Werk mit glänzender Vergangenheit wurde vom Luftfahrtpionier Pierre-Georges Latécoère erbaut. Heute ist man hier auf die Fertigung von Verbundbauteilen aus Titan und Karbonfasern sowie die Montage von komplexen Aufbauten spezialisiert. Daneben hat die Gruppe Fives im Laufe ihrer mehr als 200-jährigen Unternehmensgeschichte für die Umsetzung einiger technischer Innovationen verantwortlich gezeichnet, darunter die ersten Dampflokomotiven oder die Aufzüge des Eiffelturms. Die Gruppe Fives, die über Niederlassungen in mehr als 100 Ländern verfügt, hat im Jahr 2013 einen weiteren bekannten Akteur der Luftfahrtbranche zurück ins Geschehen gebracht: das Unternehmen Forest-Liné, das bereits vor mehr als 60 Jahren Produktionsmaschinen für die Herstellung von Flugzeugpropellern baute. Seither hat man bei Forest-Liné auch technische Expertise im Bereich der Fünf-Achs-Bearbeitung entwickelt. Für NUM sind Fives und Dassault gleichermassen langjährige, anerkannte Partner.
Da NUM viel Wert auf aktive Zusammenarbeit legt, haben diese drei Akteure ein gemeinsames Projekt rund um eine Forest-Liné V-Star in Angriff genommen. Es handelt sich hierbei um eines der Prunkstücke von Fives Machining, das Geschwindigkeit, Flexibilität und hochpräzise Dynamik vereint. Die Hochgeschwindigkeits-Fräsmaschine, die speziell für die Bearbeitung von Luftfahrtbauteilen mit grossen Abmessungen ausgelegt ist, verfügt über fünf Bearbeitungsachsen, darunter ein Gantry. Die Vorschubgeschwindigkeit Längsachse beträgt bis zu 60 m/mn, angetrieben durch vier paarig gekoppelte Linearmotoren. Die zwei sicheren Fahrbereiche, von denen jeder über sein eigenes Werkzeugmagazin verfügt, sind abwechselnd oder parallel einsetzbar. Zehn EtherCAT-Stationen mit mehr als 90 Ein-/Ausgangsmodulen, ein Werkzeugmagazin, zwei Werkzeugbruchkontrollvorrichtungen, ein RFID-Chiplesegerät und natürlich integrierte Sicherheitsfunktionen vervollständigen die Einheit. Bei diesem System handelt es sich um nichts anderes als ein Flexium+68. Ein solches System, das mit NUMDriveX-Antrieben gekoppelt ist, hat bereits seine Fähigkeit zur Steuerung derartiger Konfigurationen unter Beweis gestellt. Betrachten wir ergonomische und sicherheitsrelevante Aspekte im Detail.
Die Installation umfasst drei Bedienungfelder vom Typ FS192i, ausgestattet mit einem 19“-Bildschirm mit senkrechter Ausrichtung zur gleichzeitigen Anzeige der Bedienoberfläche (HMI) der Maschine und eines virtuellen Maschinenbedienfeldes auf einem Touchscreen. Zwei dieser Bedienfelder, die jeweils durch ein Maschinenfeld MP05 ergänzt werden, werden für ihren jeweiligen Arbeitsbereich eingesetzt. Sie sind vollständig unabhängig, jedoch kann die Maschine jeweils nur mit einem Pult gesteuert werden. Das dritte FS192i-Bedienfeld dient der Steuerung der zwei Werkzeugmagazine, damit insbesondere das Laden und Entladen mit der Messstation gewährleistet ist. Dieses Pult ist vollständig unabhängig von den beiden anderen und verfügt über alle erforderlichen Sicherheitsvorrichtungen.
Die Werkzeugmagazinsteuerung wurde gemäss den Wünschen von Dassault Aviation entwickelt. Sie ermöglicht die Nutzung von Werkzeugen mit einem Chip, auf dem bis zu 45 Parameter gespeichert sein können. Diese Parameter ermöglichen kurz gesagt die Steuerung der entsprechenden Werkzeuge, aber auch der Vorschub- und Spindelgeschwindigkeiten, Toleranzseiten, Kühlarten usw. Alle diese Daten werden auf den Seiten aufgeführt, die entsprechend den Spezifikationen von Dassault entwickelt wurden. Einige Seiten befassen sich mit der Visualisierung und Änderung der Daten, andere mit dem Beladen und Entladung der Werkzeuge.
Eine moderne Maschine ist ohne integriertes Sicherheitssystem nicht vorstellbar. In dieser Hinsicht bietet Flexium+ eine Komplettlösung, einschliesslich der Antriebsverstärker, die auf dem FSoE-Protokoll (Functional Safety over EtherCAT) basieren. Diese Lösung vereint Leistung, Einfachheit und Wirtschaftlichkeit. Die standart SPS Terminals und die Sicherheitsmodule sind nach Bedarf auf der Maschine verteilt und an denselben EtherCat-Bus angeschlossen. Die SAMX Module (Sicherheitsmodule) der Antribsverstärker sind mittels Rj45 Steckern ebenfalls an den EtherCat-Bus angeschlossen. Die gesamte Konfiguration kann mittels der Software „Flexium Tools“ programmiert werden.
Partnerschaften sind für NUM von grosser Bedeutung, erklärt uns Herr Leroy, der Verantwortliche bei Fives: „Hinsichtlich der technischen Herausforderungen dieses Projekts haben wir uns dafür entschieden, uns direkt an den Hersteller des vom Kunden gewählten CNC-Systems zu wenden. Die Funktionsweise mit SPS und externem CNC-System ist neu für uns und ermöglichte uns, bestimmte Vorgehensweisen zu vereinfachen und bestimmte Austauschvorgänge zu systematisieren, die sich normalerweise intern abspielen. Diese Entscheidung zahlte sich im Endeffekt aus, da sich NUM über die gesamte Dauer des Projekts als zuverlässiger Partner erwiesen hat. Insbesondere haben wir die Beteiligung und Reaktionsfähigkeit der Mitarbeiter von NUM zu schätzen gewusst, dank der wir auf die Besonderheiten unseres Kunden reagieren und zugleich alle festgelegten Fristen einhalten konnten.“
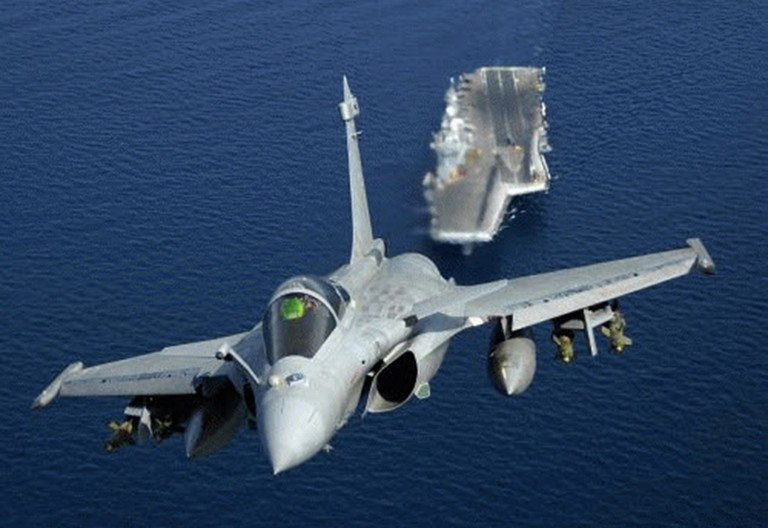
Das übergeordnete Ziel ist offenkundig die Zufriedenheit des Endnutzers, wie der Verantwortliche bei Dassault, Holtzmann, uns seinen Standpunkt erläutert: „Für uns war der ausschlaggebende Punkt bei der Wahl von Flexium+ die Investitionssicherung. Diese wollten wir mit der Auswahl eines Produktes erreichen, das mit unseren bereits vorhandenen Bearbeitungsprogrammen kompatibel ist. Selbstverständlich wollten wir auch von allen vorangegangenen Leistungsverbesserungen und technischen Fortschritten profitieren. Insbesondere hinsichtlich der Ergonomie und Sicherheit war unser Anspruch hoch. Die Mitarbeiter von NUM haben bei der Realisierung grosse Kompetenz und Sorgfalt unter Beweis gestellt und standen uns jedes Mal, wenn eine Entscheidung anlag, mit Rat und Tat zur Seite.“
Elia Barsanti, Geschäftsführer von NUM France, bemerkt hierzu: „Die Devise von NUM lautet, Maschinenkonstrukteuren Lösungen anzubieten, mit denen diese einen Wettbewerbsvorteil erreichen können. Das wurde im Rahmen dieses Projekts sehr gut umgesetzt. Die Nutzung der neuesten von NUM entwickelten Technologien und deren effizienter Einsatz ermöglichen die Steuerung der Maschine unter optimalen Bedingungen – und damit die Fertigung von modernsten Flugzeugbauteilen.“
(September 2016)