Un système de découpe au jet d’eau innovant mis au point avec l’aide de NUM
Une jeune entreprise de l’Université Technique de Chemnitz (Allemagne) a développé une machine de découpe au jet d’eau utilisant la technologie de suspension. Doté d’une efficacité et d’une qualité supérieures, en termes de performances, à celles des machines à jet d’eau avec abrasif plus conventionnelles, cette technologie se positionne entre la découpe jet d’eau avec injection d’abrasif et la découpe laser. Le système de commande NUM offre, grâce à sa flexibilité et à son ouverture, les conditions optimales pour son pilotage. Il s’agit d’une technologie de découpe jusqu’à présent inconnue dans les applications de fabrication industrielle.
« Notre objectif était de construire un système de découpe au jet d’eau compact basé sur la technologie d’abrasif en suspension qui est significativement plus puissante et en même temps plus efficace que la découpe au jet d’eau conventionnelle avec technologie par injection. Nous avons réussi ! », déclare Markus Dittrich, cofondateur et directeur général de la start-up NOVAJET et associé de recherche à l’Institut des machines-outils et des procédés de production (IWP) de l’Université Technique de Chemnitz. L’objectif est de développer un système concentré sur des diamètres de jet inférieurs à 0,4 mm et optimisé pour la production de petites pièces de précision avec des matériaux difficiles à usiner tels que la céramique ou le carbure de tungstène. Avec ce nouveau concept, les ingénieurs ont innové en matière de technologie; il n’existe pas encore de machine comparable et l’ensemble est encore en cours de développement. Les fondateurs de NOVAJET ont choisi le système NUM notamment pour sa flexibilité et son ouverture, car à ce stade du projet les optimisations et évolutions de stratégie sont courantes pour tout prototype.
De l’injection à la technologie de suspension
Tout a commencé par un projet de recherche sur la découpe au jet d’eau avec abrasif et un diamètre de jet d’environ 0,3 mm. « Nous avons constaté que la puissance de coupe du jet avec la technologie conventionnelle par injection diminue exponentiellement à mesure que nous réduisons le diamètre du jet. Au fur et à mesure de cette réduction, nous n’arrivions plus qu’à découper des tôles minces », explique Markus Dittrich tout en fournissant l’explication technique : « Dans les systèmes jet d’eau avec abrasif conventionnels, l’eau est amenée à une pression comprise entre 3000 et 6000 bars dans une chambre de mélange. Cela crée un effet Venturi qui aspire l’abrasif sec d’un récipient de stockage et le transporte avec le jet d’eau. L’accélération de l’abrasif seul consomme environ 30 % de l’énergie initialement introduite dans l’eau », explique M. Dittrich. De plus, ce type de mélange introduit beaucoup d’air dans le jet et distribue principalement l’abrasif sur le pourtour du jet. Les deux phénomènes réduisent le taux d’enlèvement.
Une alternative est la technologie par suspension, une technologie de découpe qui a jusqu’à présent été davantage utilisée pour des applications demandant moins de précision. Elle est utilisée par exemple dans le démantèlement de centrales électriques. L’eau et l’abrasif sont mélangés initialement pour former une suspension, celle-ci est ensuite mise sous haute pression dans une chambre adaptée puis dirigée vers la buse de découpe qui va la focaliser pour former un jet doté d’une grande vitesse. Un projet de suivi mené à l’Université Technique de Chemnitz avec les partenaires industriels ANT AG et ATECH GmbH a déjà prouvé que cette technologie a le potentiel d’être utilisée sur une machine-outil. « Il est possible d’obtenir une augmentation de performance de plus de 300 % par rapport au procédé par injection », résume M. Dittrich. Concrètement : avec une pression de 1400 bars et les mêmes conditions, les tests ont montré que la découpe était au moins trois fois plus rapide et plus précise qu’avec la technologie par injection à 3000 bars. C’est également le cas pour la céramique. Cet accroissement de performances est dû à la qualité du jet, car celui-ci est exempt d’air et l’abrasif est distribué dans le centre du jet. De plus, l’erreur d’angle typique du jet d’eau est nettement plus faible avec la découpe en suspension et des diamètres de jet de 0,2 mm ont déjà été obtenus lors d’essais.
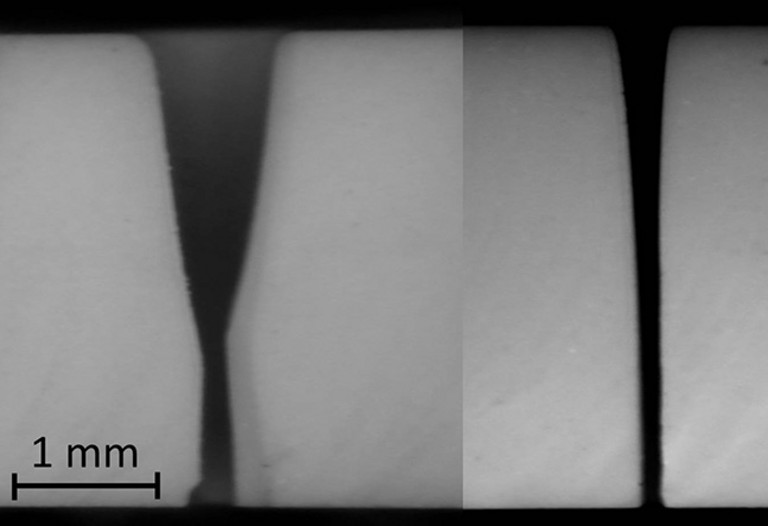
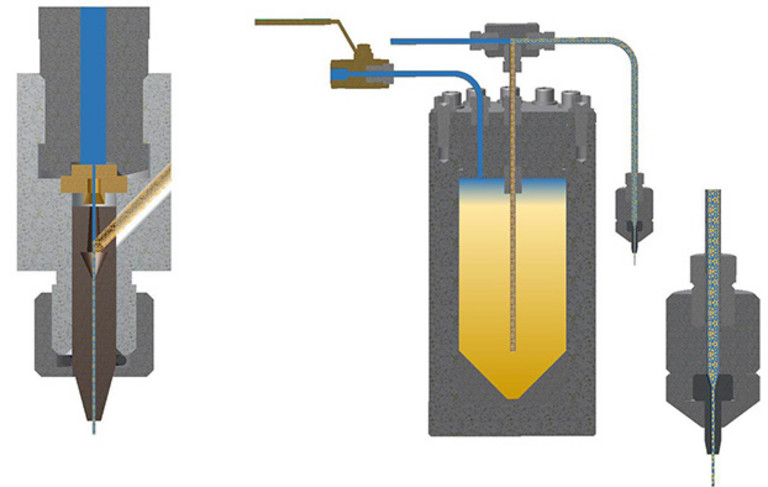
Une machine pour l’industrie
Le système est en cours d’optimisation. La conception de l’installation est très compacte et tous les composants, des pompes au réservoir à haute pression en passant par la table de travail et le système de coupe, sont réunis en une seule unité. La machine fonctionne avec une pression d’eau de 1500 bars et la zone de travail de 350 mm x 510 mm est suffisante pour la fabrication précise de petites pièces. Le réservoir à haute pression est conçu de telle sorte qu’il est possible d’obtenir un temps de coupe pur d’environ 20 minutes avec un seul remplissage et un diamètre de jet de 0,4 mm. Ensuite, lors de la phase finale de développement, ce réservoir sera automatiquement déchargé, rempli et pressurisé à nouveau. Le système est évidemment un peu plus complexe que ce simple énoncé de principe. Par exemple, un circuit principal avec de l’eau pure provenant de la pompe haute pression est couplé à un circuit secondaire pour la suspension du réservoir haute pression.
De plus, la composition homogène du jet nécessite une technologie de contrôle plus complexe. « Nous avons un assez grand nombre de vannes qui doivent être adaptées les unes aux autres. Il y a également une pompe haute pression intégrée. Et nous avons des systèmes de surveillance de processus qui surveillent à la fois le jet, le mélange abrasif lui-même, ainsi que le réservoir haute pression », explique Markus Dittrich. Ces systèmes de surveillance n’existent pas dans la technologie par injection et, par conséquent, il n’existe pas de système de contrôle prêt à l’emploi qui convertisse les signaux des systèmes de surveillance en entrées de régulation pour l’ensemble du système.
« Pour le choix du système de commande, il était très important pour nous que tous les paramètres, de la pression de l’eau, à la commande des axes, en passant par le remplissage automatique et jusqu’à ceux de la tête de coupe, soient accessibles au système de commande. La surveillance de la tête de coupe fournit un signal qui doit permettre, en temps réel, de réajuster la commande de la pompe haute pression. L’établissement de ces liens en arrière-plan est très important pour notre technologie », déclare Markus Dittrich.
NOVAJET a choisi d’utiliser la plate-forme CNC de NUM pour plusieurs raisons. Premièrement, les commandes NUM sont standard sur les rectifieuses du marché ciblé qui est celui de l’industrie des matériaux haute performance ; d’autre part, il existe déjà sur le marché des systèmes de découpe au jet d’eau avec commandes NUM, ce qui signifie que des composants de configuration appropriée sont disponibles pour la découpe au jet d’eau ; et enfin, NUM fournit un ensemble complet du pupitre PC aux moteurs en passant par la commande CNC et les variateurs (sans oublier le support efficace des services d’ingénierie).
Expérience positive de la mise en service
La décision de choisir NUM s’est avérée être la bonne, y compris pendant la phase de démarrage. Un technicien de NUM a passé deux jours à Chemnitz pour assurer l’intégration des moteurs et variateurs, afin que les entraînements soient rapidement opérationnels. Grâce aux connaissances acquises lors d’une semaine de formation, les fondateurs de NOVAJET ont été en mesure d’achever en deux semaines la mise en service restante et par leurs propres moyens. « Nous avons cependant toujours eu la possibilité d’obtenir une assistance téléphonique. Nous avons pu éliminer toutes les difficultés assez facilement grâce à la téléassistance », explique Stefan Seidel, le co-fondateur en charge de la partie technique. Pendant la phase de mise en route de l’installation, la programmation des boucles de réaction s’est également avérée très aisée. L’accent est mis en particulier sur l’accès direct aux nombreuses fonctions du système de commande.
« Lors de la mise en service, nous n’avons cessé de remarquer des détails que nous devions modifier ou adapter », explique M. Dittrich. « Puis, bien sûr, nous avons également dû parfois adapter les fonctions du système de contrôle. Si nous avions dû nous fier à un fabricant qui facturait le moindre conseil ou avait besoin de longues boucles de décision pour la moindre adaptation, le projet se serait vite retrouvé en grande difficulté », résume Markus Dittrich.
(Septembre 2019)