Innovative riveting machines for enhanced productivity and manufacturing quality on aircraft doors
CYBERMECA, located in Fontenay-le-Comte on the French Atlantic Coast, is a company that is part of the Ledoux Group. The group offers its customers diverse industrial skills in a wide range of fields such as engineering, mechanical design, automation, programming, hydraulics, sheet metal work, painting, assembly and geometric positioning, in addition to manufacturing electrical cabinets. The broad scope of its expertise has contributed significantly to the success the group has experienced over the past 12 years.
In collaboration with leading industrial companies, CYBERMECA provides joint project management in fields such as aeronautics, automobile, aerospace and defense – which all require exacting standards. Its success can be attributed entirely to its multi-skilled workforce working in close collaboration with companies such as NUM, a pioneering company in the CNC field which has specialized for more than 50 years in automating high-end, specialized machine tools. Over the past few years, NUM France, in particular, has worked on a number of highly technical aeronautics projects, including the Dassault Falcon private business jets and the famous Rafale multi-role fighter aircraft.
The new riveter described in this article is designed for manufacturing aircraft doors. During the design phase, the main challenges CYBERMECA and NUM faced were reducing production time, facilitating processes and optimizing work quality. To achieve this, the machine is equipped with twelve digital axes, a riveter head and a state-of-the-art operator console. It allows for complex riveting cycles to be run at a high rate, with an unparalleled level of reliability. Each cycle takes only six seconds to complete! The entire production process takes place under video surveillance through cameras allowing for specific work stations to be viewed.
The machine is driven by the Flexium+ CNC platform. The 12 axes are equipped with NUM SPX single drive-to-motor cables and NUMDrive X servodrives equipped with NUMSafe safety functionality. A number of different functionalities devised by the LEDOUX Group are available as an option (VAO, electrical heads, electrical consoles, a B axis, the use of different types of rivets, etc.).
The LEDOUX Group and NUM’s pooled experience gained over many years concerning the development of specific applications has offered great flexibility in producing riveters, allowing for solutions to be optimized in line with customer requirements. The machine’s riveting cycles and movements have been vastly optimized thanks to the continual technological progress made by both partners.
“Particular attention is paid to choosing high-quality components and selecting experienced partners such as NUM to ensure we supply our customers with a reliable machine. This reliability is recognized by our customers, who are key players in the aeronautics fuselage manufacturing sector where production speed requires high-performance equipment”, explains Didier Ledoux, Managing Director of the Ledoux Group.
But the experience contributed by both partners has also allowed the duration of the entire process - which includes positioning of the door, drilling of the rivet hole, positioning of the rivet, securing and compression of the rivet head - to be reduced to only six seconds. The crucial role played by the thousands of rivets fitted to aircraft requires a process of optimum quality. It is easy to imagine that the innumerable temperature and pressure changes as well as the resulting expansion and contraction that aircraft undergo over their lifetime puts the rivets to the absolute test.
CYBERMECA and NUM have worked together for almost four years to develop this special riveter for aircraft doors, which has been fully aligned with customer requirements. The Airbus A320 is a very popular aircraft requiring an increase in production rates, which in turn calls for a faster riveting process, naturally without compromising quality. Riveting is a crucial component in aeronautical safety.
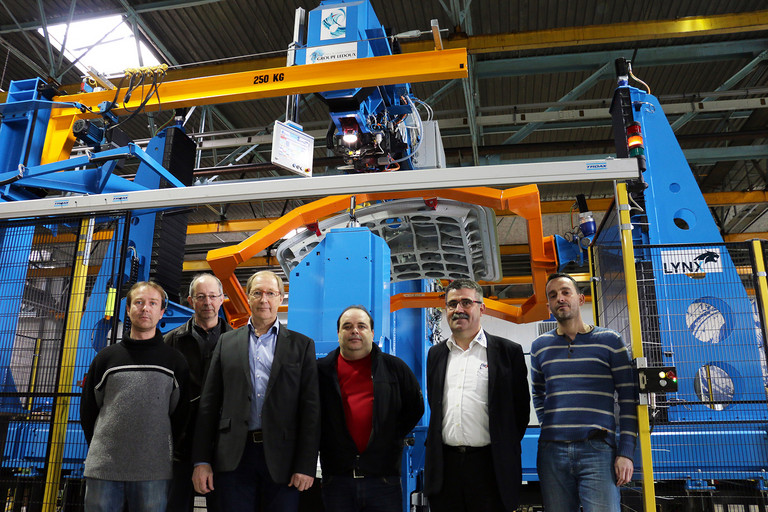
From the outset of the project, both companies were faced with a major challenge: the machine needed to be developed and assembled around the finished product. This product, namely the aircraft door, was produced prior to the design of the riveters and had, up until that time, been manufactured on other machines following different processes. The riveting machine therefore had to allow for orifices to be drilled according to the existing positioning of the rivets on the doors, bearing in mind that no change or adaptation would be possible. This also explains the specific design of the machine. The aircraft door is assembled on a specially developed frame supported by two arms. These arms raise and rotate the door to the desired angle on both sides, ensuring that the driver is able to carry out the drilling and riveting work. The driver still works in a vertical direction with partially adjustable stability, unlike the standard movements of the usual X, Y, Z axes.
The technical progress made during the development of this riveter has already been further utilized for the design of larger machines able to carry out riveting on entire sections of fuselage. Despite the fact that specialized machines are used to execute key tasks such as riveting are rarely in the limelight, they are vital. Their flawless quality allows for complete safety in flight; spare a thought for this during your next flight.
(September 2016)