20-year partnership helps maintain tool grinding leadership
Star Cutter Company is a world leader in carbide and preform manufacturing, cutting tools and CNC machines for tool/cutter grinding and hob sharpening. Founded in Detroit back in 1927, the company nowadays operates six manufacturing facilities at strategic locations throughout Michigan. Since 1998, Star Cutter has partnered with NUM for cooperative development of application-specific CNC hardware and software. During the course of this nearly 20-year collaboration, the two companies have advanced cutting tool machine technology significantly – Star Cutter currently manufactures seven highly specialized lines of machine tools, six of which are based on NUM’s CNC systems.
Star Cutter originally used Fanuc controllers for its machines. However, with a goal to bring it’s customers even more capability and ease in realizing complex tool forms, to bring more flexibility and speed in integration of third-party motors and to simplify development of control software, the company sought to transition from a proprietary control scheme to a more open CNC platform.
According to Bradley Lawton, Chairman of Star Cutter Company, “NUM was an obvious choice. The company is renowned for the open architecture nature of its CNC solutions, and has done much to remove the ‘black box’ mystique that is endemic to many of the competitive CNC products on the market. And the quality and reliability of NUM’s products is excellent, which is extremely important to us – over 99% of the machines that we have produced in the past 20 years are still in everyday use. On top of that, NUM’s customer support is superb and we enjoy very responsive and helpful technical help”.
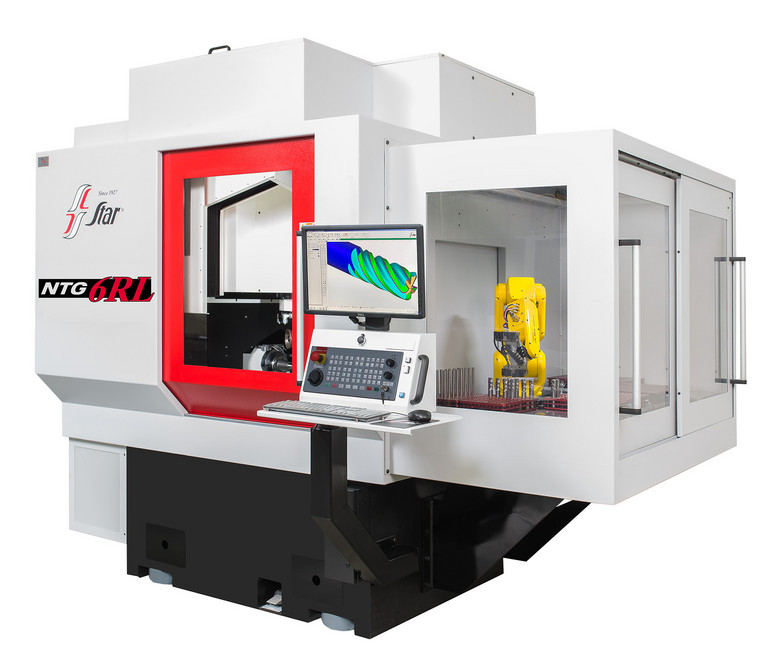
NUM and Star Cutter’s partnership has undoubtedly created dividends for both companies, as well as for their customers and machine end-users. Starting with its ETG and PTG series of tool and cutter grinders – which now have an installed base of more than 200 – Star Cutter has steadily migrated nearly all of its CNC machines across to NUM’s control technology. About seven years ago, the company launched its highly successful ETG and NTG series of rotary tool grinders, including the advanced full linear NTG-6RL 5-axis grinder, which handles fluting, relief grinding and automated wheel change. All of these machines are based on NUM’s CNC hardware and NUMROTOplus software.
Currently under development, Star Cutter’s next generation machines are based entirely on NUM’s powerful Flexium+ CNC platform. The NUMDrive X modules that form part of this high-end CNC solution provide the drive flexibility that is needed to accommodate a variety of third-party linear and direct drive torque motors, as well as high frequency grinding spindle motors. As a consequence, the machines are capable of very high grinding and surface finish accuracies, combined with unprecedented grinding speeds, and promise to be the most productive that Star Cutter has ever produced.
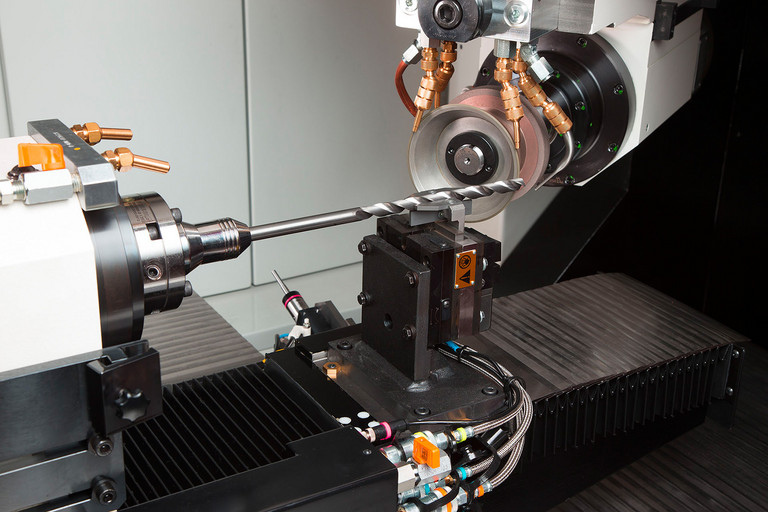
Steven Schilling, General Manager of NUM Corporation in Naperville, Illinois, points out, “The higher bandwidth of the NUMDrive X servo drive and improved internal processing of NUM’s Flexium+ CNC platform, which is now managed by double-precision IEEE 754 floating point, gives capability down to sub-nanometer accuracy. This provides manufacturers like Star Cutter with the opportunity to create machines that can grind even the smallest tools with superb accuracy.”
Another key attribute of the Flexium+ platform is that it can run grinding programs as large as 40 MB directly from the NCK memory. And for very complex grinding cycles, the CNC system can execute cycles directly from the system’s disk drive, via a high speed data transfer protocol. This increased capacity and speed helps Star Cutter’s customers expand their CAD/CAM grinding operations. Whether it be the processing of advanced materials and aerospace components or medical devices and tools.
Star Cutter’s new grinding machine also features a novel servo-assisted popup mechanical steady rest. This makes full use of the ‘detachable axes’ facility of Flexium+ systems equipped with NUMDrive X modules. It enables end users to simply place the rest into the machine for the production of longer parts, and to quickly remove the full motor/mechanical assembly when it is not needed.
Focusing on an intuitive user experience, the operator station has been completely redesigned to reduce button pushing, and to simplify machine setups and daily operations. The optional 6 axis robotic part loader essentially programs itself from the NUMROTO tool files, requiring minimal user inputs. The robot can be set to alert shop personal of process completion or issues encountered during unattended production.
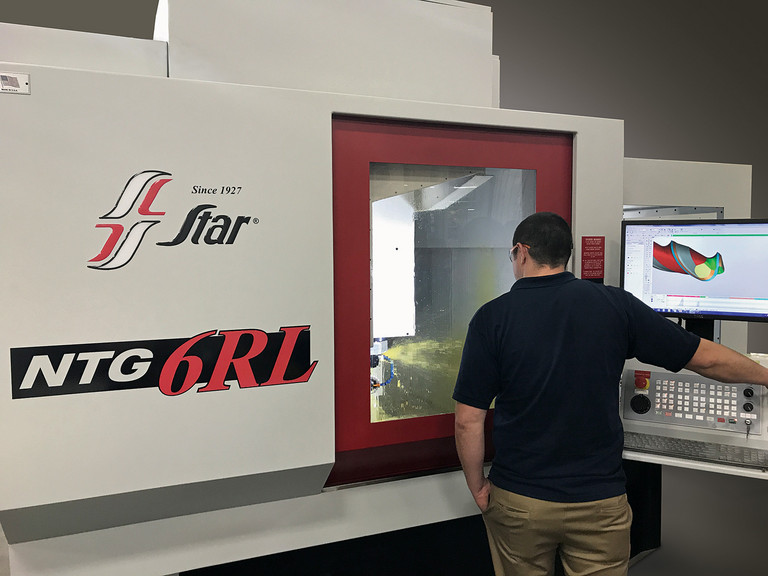
The new machine is also designed for ease of integration with other forms of industrial automation and handling robots. NUM's Flexium+ platform offers a wide variety of system communication busses, including EtherCAT, CAN and EtherNet. Measured process or post-process data can be fed back to the CNC system's NUMROTO software to provide on-the-fly corrections, facilitating adaptive real-time control of the entire grinding process. Shop floor data can even be shared easily with the rest of the plant and to the cloud with NUM's built-in MTConnect interface.
Thanks to Star Cutter and NUM, full lights-out tool and cutter grinding is now a practical possibility.
(September 2017)