Making the old as good as new – thanks to retrofitting. Increasing the efficiency of an underfloor wheel grinding machine through a new design.
In the municipal transport services of the city of Zurich (VBZ), new types of trams have been recently introduced for daily use. The lower number of axles and smaller wheel diameters of the low-floor vehicles lead to higher loads on the wheels and thus to greater wear as in conventional rail vehicles. Worn wheel tyres could also lead to impaired riding comfort. Only through the mechanical reworking of the tyres (re-profiling) can this problem be remedied. VBZ and the company EMOTEC, in close collaboration with NUM, have come up with an innovative and reliable solution to get the wheels running true again.
These wheelsets will be reworked in the VBZ maintenance hangar in Zurich-Oerlikon. With the 1991 underfloor machine of the Kellenberger company that was used previously, the wheels were ground through a form grinding wheel. This process is very time-consuming for heavier degrees of wear, since sometimes several millimetres of the tyre must be removed in order to bring the wheels to a uniform diameter. In addition, the upkeep of the nearly 20-year-old control unit could only be done at great expense.
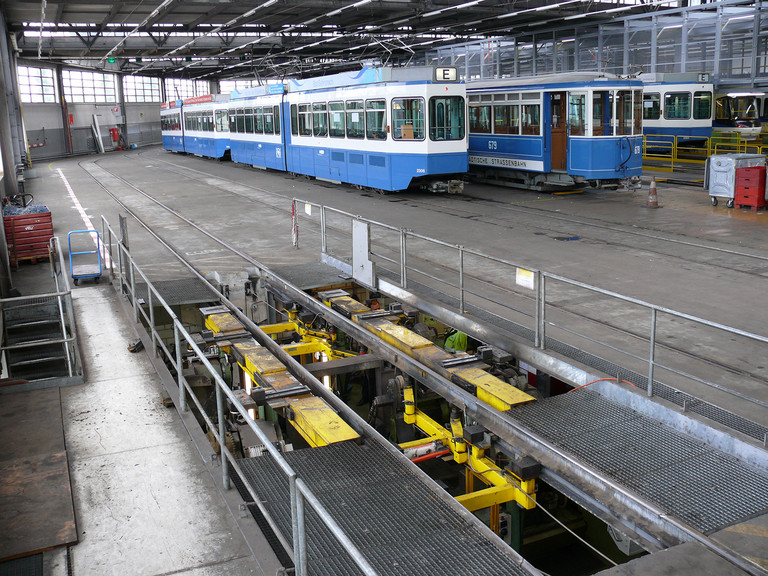
The higher wear on the tram wheels requires greatly increased efficiency of wheelset machining and the manufacture of different profiles on the tyres. The VBZ trials first determined the fundamental feasibility of performing lathing on the existing grinding machines. Based on this, the Swiss company EMOTEC, in collaboration with VBZ, developed a concept for the enhancement of the machines with NC-controlled turning attachments for precision turning. This construction enables a complete bogie with four wheels to be relathed or reground in a clamping. Working closely with NUM, a controller design was developed which also included the replacement of the existing control unit.
The system also needed to be equipped with a modern control panel that would allow uncomplicated and reliable operation of the machine. The design features two Axium controllers with a total of 16 axles, two FSi-151 control panels and NUM’s MDLU3 drive technology, which meet all these requirements. NUM developed the entire control and visualisation software. Such a machine retains the advantages of the grinding process while also meeting demands for performance and flexibility, since the wheels are trimmed before the grinding process or exclusively turned.
The advantages of turning are, above all, the clearly shorter machining times, primarily with heavily worn tyres, and re-profiling of the tyres including the flange and the back of the wheel. Other advantages include the option of machining different tyre profiles without having to adapt the tools, as well as optimised turning processes for roughing and finishing. It quickly becomes clear that, for such combined machining, high demands are placed on the control unit. Two completely different machining processes must be made operable in such a way that the machine operator is provided with clear procedures to ensure the production sequences are clearly understood.
For the success of this project, the use of modern materials for the tools, a machine construction based on the requirements, and not least of all the use of a powerful control unit with optimally set drives were instrumental. EMOTEC and NUM have demonstrated that the retrofitting of an existing machine using novel ideas can indeed compete with the purchase of a new machine. Experience the result first-hand when you take one of the many trams in the city of Zurich and enjoy a gentle ride.
(August 2010)