Retrofit of a Bevel Gear Hobbing Machine for Manufacturing Straight Gears
If the cost difference is small, the customer will always choose to purchase a new model machine rather than a retrofitted one. However, when the price difference becomes greater, the conversation changes dramatically. This is exactly why thirty years ago the company Lanzi – Manutenzioni e Retrofit from Emilia began offering retrofits on machines, and specifically on gear cutting machines thanks to an ingenious idea of Gian Luigi Lanzi, from the second generation of the family. The retrofit challenge is far from simple, but one which has evolved over the years relying on a technological partnership with NUM.
Retrofitting a gear hobbing machine, including changing the operating concept, is a very complex operation that requires specific know-how and technical skills at the highest level.
The company Lanzi - Manutenzioni e Retrofit was founded over fifty years ago in 1964 by Francesco Lanzi who specialized in the maintenance of traditional machines like lathes and milling machines. About twenty years later, Luigi Lanzi, from the second generation of the family, recognized a new and untapped market niche, and gradually shifted the company’s core business from the original segment to the field of modernizing gear cutting machines. This is when the company first began collaborating with NUM. The new focus of the company, based in Ozzano dell’Emilia (province of Bologna), is still the same today: retrofitting gear cutting machines, with particular attention to the bevel gear sector, and also including spiral and spur gears.
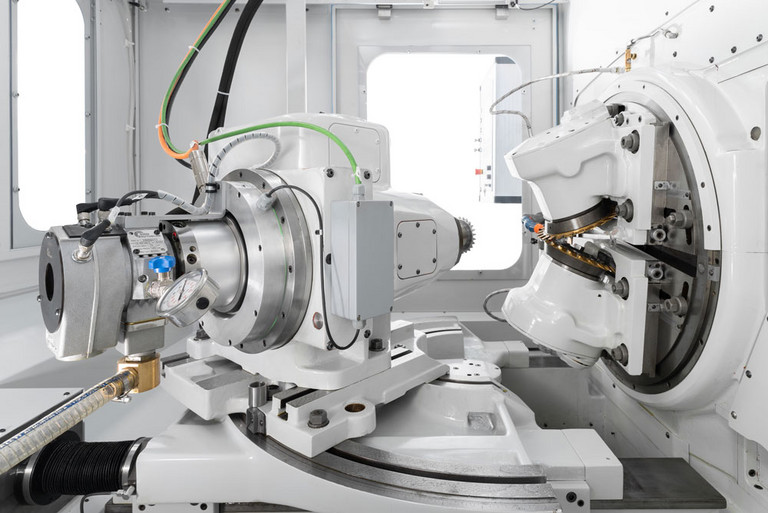
“There is a significant difference between the purchase price of a new machine and the retrofit of a hobbing machine”, explains Federico Lanzi, who has been managing the company alongside his father in the third generation since 2007. “Of course, the retrofitted machines have a slightly lower output, typically a production deficit of about 30%, but that doesn’t change the fact that the end user can buy three [or], four hobbing machines [for the same budget] instead of just one. So, if the customer does not have space problems in his plant, it is much more advantageous to buy a retrofitted hobbing machine.” It is also interesting to ask about the service life of a retrofitted gear hobbing machine. This is almost as long as that of a new machine, if not longer, due to the rather large cast iron machine beds with which the original machines are equipped in most cases. Today, when a hobbing machine leaves the Lanzi factory after a retrofit, it is basically a new Lanzi brand machine, CE certified and equipped with Industry 4.0 functions. This means that anyone who decides to buy such a machine can benefit from all the advantages they would get if they had bought a new machine.
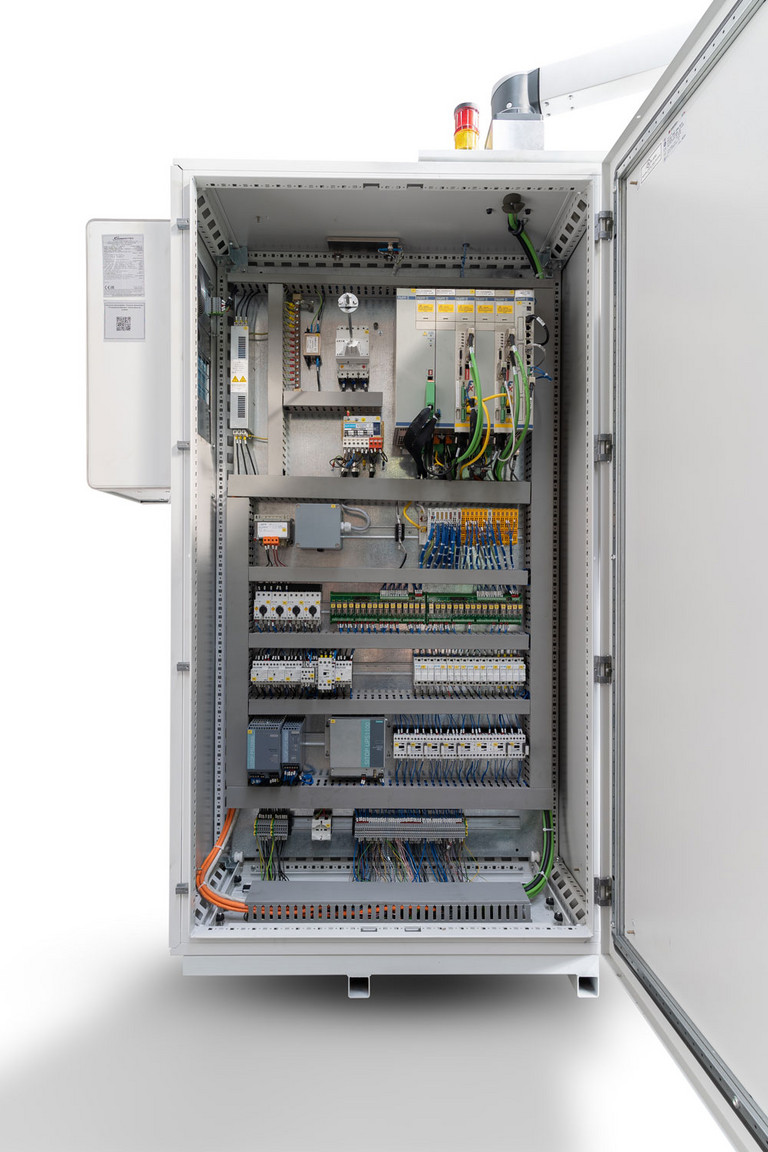
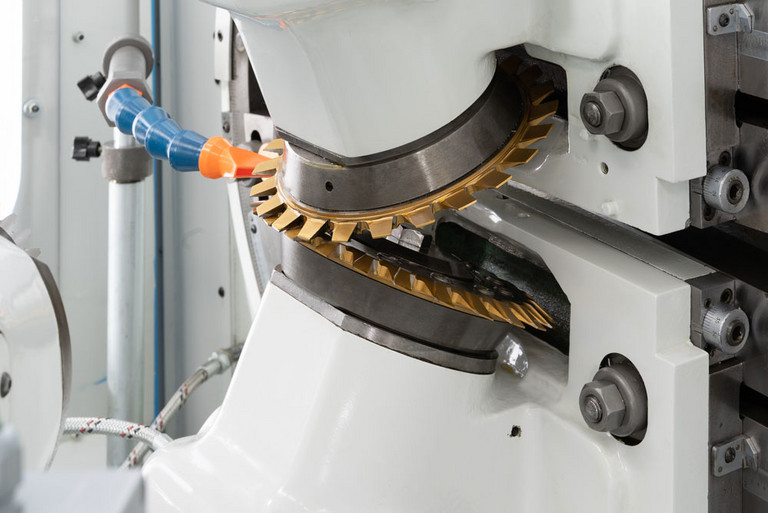
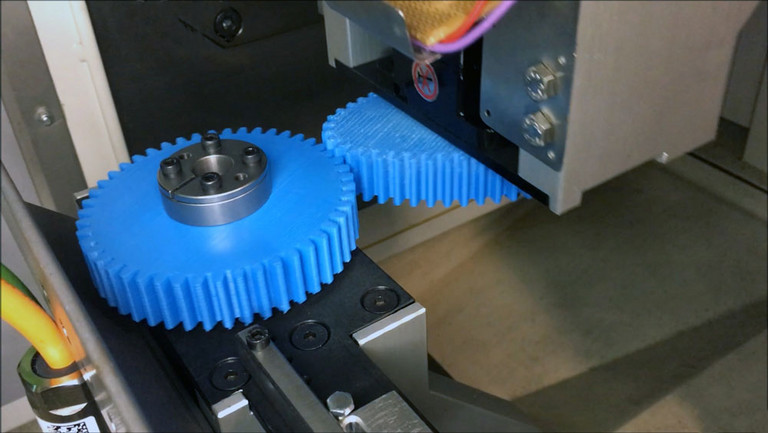
There are many key performance gains when retrofitting a gear cutting machine originating from the 1960s and 1970s. First of all, it can be noted that the new retrofitted CNC machine performs the same machining operations as the conventional mechanical machine, but - quite clearly - with an exponentially higher output. This is thanks to a reduction in set-up and production time, and with a significantly higher quality of the finished gear. “Compared to a conventional machine”, adds Marco Battistotti, Managing Director of NUM NTC Italy, “the CNC machine is also much more flexible in terms of programming. This is because Lanzi has developed their own HMI (operator interface) using functions from our system. This makes it much easier for the specialist to create the machining program.”
The retrofit of a hobbing machine always starts with an initial evaluation phase to understand whether it makes sense to carry out the retrofit at all from a technical/economic point of view. “After an initial analysis, the machine is completely disassembled and repainted”, explains Federico Lanzi, “so that we can then move on to the next phase, which is one of the most important. It consists in fitting the latest generation motors - NUM in our case - to the old mechanics.” The machine is then connected to the new electrical cabinet, which houses the numerical control system that controls the machine’s three axes.
The long-standing collaboration between NUM and Lanzi has deepened over the years through various projects. The most recent project was the retrofit of an old bevel gear hobbing machine for straight-toothed work pieces. For this, NUM supplied the complete CNC system NUM Flexium+ 8 with all safety functions, MDLUX drives and BPX motors.
“Originally”, says Federico Lanzi, “this machine consisted of two milling heads where the cutting edges were synchronized so that the two sides of the workpiece’s teeth could be machined simultaneously. The focus of our project was to design the two heads with direct drives inside, in order to be able to achieve a higher cutting speed and eliminate the mechanical backlash, which is usually the main cause of machining errors. With this implementation, we were very optimistic that in the future we will be able to work with carbide cutters, a modification already used in the spiral bevel gear hobbing machines. The special feature of tungsten carbide is that it can significantly increase the cutting speed and thus the machining feed rates, which shortens production times. One challenge in implementing this project was to keep the two cutting heads synchronized. Originally, they moved synchronously because they were mechanically connected and drive by a single motor. However, once they were electronically controlled they became two completely separate heads, and NUM’s support was critical to keeping them synchronized.” To this end, NUM has developed a special function - Electronic Gear Box. It ensures that the two heads remain fully synchronized at all times so they don’t collide or misalign with each other which would eventually cause a malfunction.
Much of Lanzi’s energy went into increasing machine performance, for example by replacing the crown wheel spindle with a direct-drive ball screw for moving the carriage. It also added optional extras that the conventional machine did not have, such as the connection of robots for loading and unloading the work pieces, and programmable work piece clamping and cutting force controls. On top of all this is the issue of sustainability. “Today we are trying to make people aware of the importance of retrofitting also from the point of view of sustainability”, concludes Federico Lanzi. “Upgrading an older machine instead of scrapping it is undoubtedly a much more sustainable decision rather than buying a new one.”
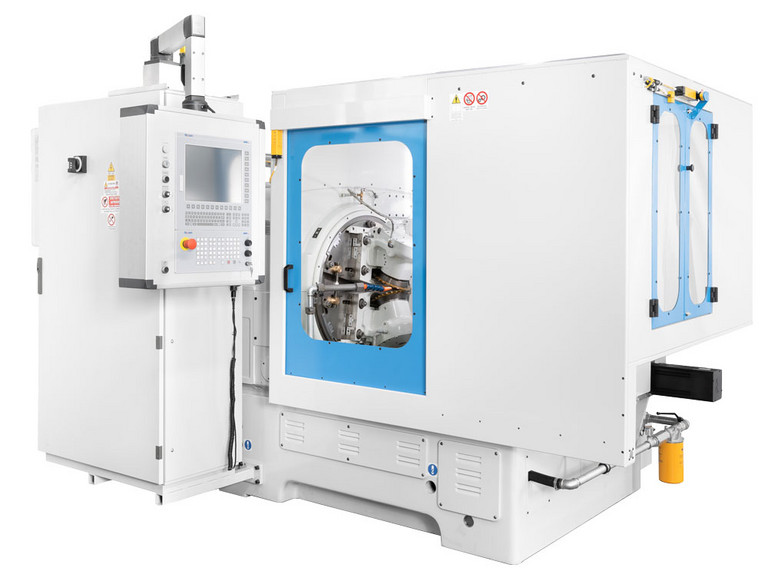
(September 2023)